Featured Listings
- PTPShopy
- TLC Autocentres
- Completely Hydraulic Kent
- MTC West London Removals
- MTC North London Removals
- Managed Print Experts
- Equity Release and Mortgage Partnership
- Myndstone Builders
- Oxford Magic Walking Tours
- Elite Loft Conversions
- Synergy SW Ltd
- Zephyr X
- Harewood Dental Surgery
- Redirack
- Check It Scaffolding
Other Business Categories
- Copywriters Bedfordshire
- Conference Centres & Room Hire Bedfordshire
- Internet Services Bedfordshire
- Couriers Bedfordshire
- Removal Companies Bedfordshire
- Gyms & Health Clubs Bedfordshire
- Hairdressers Bedfordshire
- Laser Clinics Bedfordshire
- Fishing Businesses Bedfordshire
- Jewellery & Gift Wholesalers Bedfordshire
- Antique Clocks Bedfordshire
- Baby Shops Bedfordshire
- Aerials and Satellites Bedfordshire
- Supermarkets Bedfordshire
- Taxi Cabs Bedfordshire
AM Philpot (Hard Chrome) Ltd in Bedfordshire, England
AM Philpot (Hard Chrome) Ltd with information like telephone number, maps, postcode, address and related useful information.
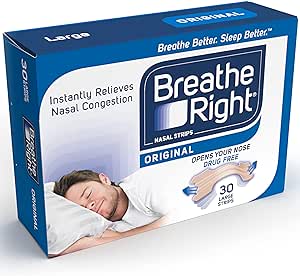
AM Philpot (Hard Chrome) Ltd
Address: Unit D Cradock Road Industrial Estate Luton Bedfordshire United Kingdom LU4 0JF
Postcode: LU4 0JF
City/Town: Bedfordshire, England , UK
Main Phone:01582 571234
Website:www.amphardchrome.co.uk
Category:General Services
Get simple code & place at your website

Description
AM Philpot (Hard Chrome) Ltd
Primarily based in Luton, Bedfordshire, AM Philpot (Hard Chrome) Ltd employ 19 staff and undertake a range of engineering services including HARD CHROME PLATING and CNC GRINDING.
Established in 1902 the company has a long and prestigious history which is detailed more fully here.
A significant amount of our work involves the reclamation of used and worn parts such as MACHINE SPINDLES and HYDRAULIC CYLINDERS. Our hands on and dynamic structure allows us to handle jobs that other larger companies might turn away.
We have also developed a specialist division within the company to supply MECHANICAL PARTS for the canning industry including SPINDLES, ROLLERS and AXLES as well as INKING COMPONENTS. These canning machines are the type used to press and print beer cans.
More information...
Hard Chrome Plating
We offer a HARD CHROME PLATING service using Chromic Acid - Chromium Trioxide Flake from Elementis. Our solution is made up of 250g/l CrO3 and Sulphuric Acid at a 100-1 ratio.
Background: Hard chrome plating, sometimes referred to as functional chrome plating, can be applied in thick layers for heavy industrial applications. It increases wear and corrosion resistance whilst creating a low co-efficient of friction. With abrasion being the most common and destructive wear process found in industry, hard chrome has the potential to solve many problems in pumps, valves, bearings, etc. throughout a wide range of industries; including pharmaceutical, chemical, oil and gas, textiles, printing, food, mining, and countless others.
One application for hard chrome is the refurbishment of worn components where the metal has been lost through wear or been manufactured under size, or, even where there has been an excessive distortion during the hardening process. This application usually requires a thicker deposit and components are pre-chrome ground then a suitable deposit of hard chrome is applied before they are ground back to original sizes and tolerances.
Process: Hard Chrome plating is an electrolytic process utilising a chromic acid-based electrolyte. The component requiring plating becomes the cathode and, with the passage of a DC current via anodes, chromium metal builds on the component surface.
More information...
Flash Chrome Plating
We offer a flash chrome plating service based on Chromic Acid - Chromium Trioxide Flake from Elementis. Our solution is made up of 250g/l CrO3 and Sulphuric Acid at a 100:1 ratio.
Process: Flash hard chrome plating is an electrolytic process utilising a chromic acid-based electrolyte. The component requiring plating becomes the cathode and, with the passage of a DC current via anodes, chromium metal builds on the component surface.
Background: Flash hard chrome plating, also referred to as functional chrome plating, is applied as a thinner layer. It is ideal for close tolerance applications where an excessive build up of chrome is undesirable and where the requirement is to provide a durable hard wear-resisting surface.
Applications: Flash Hard Chrome plating has many typical applications, some of which are detailed below:
Wire wound rods for paper coating Seal areas on pump or drive shafts Conveyer guide rails and rollers Plastic extruder screws Hydraulic rams and cylinders Print rollers More Information...
Metal Spraying
We offer a Metal Spraying service using a number of Sulzer Metco12E (Wire fed) guns and Sulzer Metco 5P mk11 (powder fed) guns.
A wide range of coatings can be applied including high carbon steel right through to stainless steel, copper, bonze, aluminium, molybdenum and lead based materials. Applications are almost endless, but a few examples include seal diameters, machine spindles, bearing surfaces & print rollers.
Fast Turnaround: Because metal spraying can be a fairly fast operation turn around times can be greatly reduced when to compared to electroplating (i.e. our hard chroming process). This is particularly useful for emergency services such as spindle repair on machine breakdowns. Metal spraying is also useful for repairing work that has been machined incorrectly or has been unexpectedly damaged. Thick coatings can be built up and subsequently ground back to tolerance required.
Overview:
The flame spraying process uses a heat source of oxygen and acetylene. The material to be applied is fed into the flame in the form of a wire then compressed air is used to atomise the molten metal and accelerate the particle to the substrate.
The combustion powder process uses a similar technique but a powder replaces the wire as the feedstock, thus, a larger selection of spray materials is available, as not all spray materials can be manufactured in wire form.
More Information...
CNC & Universal Grinding
We have built a reputation by providing high quality and quick delivery at a competitive price. The main advantage of CNC grinding, whether it is between centres, chuck or fixture application, is the ability to perform multiple operations in one set-up. Our CNC Jones & Shipman grinders can grind a number of O/D?s on a stepped shaft in the same operation, or likewise multiple bores, thus achieving perfect concentricity while dramatically increasing our efficiency, and allowing us to reduce cost to our customers.
CNC Universal Grinding Facilities: These machines are used mainly for volume production work to meet the rigorous demands and exacting requirements of high production grinding.
We currently operate two CNC grinders with capacities as follows:
Jones & Shipman Format 15 350mm Dia. x 1000mm B/C
Jones & Shipman Format 15 250mm Dia. x 700mm B/C
Both fitted with universal swivelling wheel head for external and internal grinding.
More Information...
Internal Grinding
As well as internal grinding via our universal grinders we also have a Churchill internal grinding machine with a capacity of 715mm dia. x 458mm maximum depth of bore. As this is a dedicated internal grinder with a larger capacity it enables us to produce high quality finishes beyond the capacity of the universal grinders. It is fully equiped with faceplates, chucks, steadies and 3 various spindles accommodating numerous quills.
Capacity: We operate the following.
Churchill grinder 715mm dia. x 458mm depth of bore. Universal grinding capacitiy of 355mm dia. x 200mm depth of bore. Abrasives: We offer a range of abrasives to suit material types and finishes including both manufactured and natural abrasives such as corundum, diamond, silicon carbide and aluminium oxide.
More Information...
Centreless Grinding
We are able to offer centreless grinding, both through-feed and plunge grinding.
Through-Feed Grinding: Can be utilised for bars, shafts, and other components. Parts of more than one diameter can be ground using the through-feed process if the diameter being ground is the largest diameter on the part and it comprises the majority of the overall part length. If multiple diameters need to be ground on the same part, this form of grinding can often be combined with other grinding processes to carry out the customer?s requirements efficiently and cost effectively.
Plunge Grinding: Is generally used for components that require grinding up to a shoulder or a larger diameter. The work-piece moves in axially between the grinding wheels, stops for the grinding operation, and then moves out again. Again this form of grinding offers the customer a cost effective, efficient service.
Principle: The principle of centreless grinding can be seen in the diagram below. Two wheels are used, the larger one operating at regular grinding speeds which does the actual grinding, and a smaller regulating wheel. The regulating wheel revolves at a much slower surface speed - usually around 50-200 ft/min, and controls the rotation and longitudinal motion of the work piece. For through-feed grinding, one or both wheels of the centreless grinding machine are canted out of the horizontal plane, this imparts a horizontal velocity to the work piece, so that outside feed mechanisms are not necessary. The work piece is held against the work-rest blade by the cutting forces exerted by the grinding wheel and rotates at approximately the same surface speed as that of the regulating wheel.
More Information...
2 Piece Canning Components
Within our manufacturing facilities we are able to supply components used within the two piece can production industry. Whether they are a ceramic coated / hard chromed or a plain component, we have the experience and expertise to provide high quality replacements. A few of the parts we currently supply follow:
Bodymaker rams Trimmers Cupper parts Necker parts Washer parts Modified components can be supplied to individual plants
We also offer a repair service for a lot of components, providing a cheaper alternative to new where available.
Contact Us
" For Further Information CLICK HERE "