Featured Listings
- PTPShopy
- TLC Autocentres
- Completely Hydraulic Kent
- MTC West London Removals
- MTC North London Removals
- Managed Print Experts
- Equity Release and Mortgage Partnership
- Myndstone Builders
- Oxford Magic Walking Tours
- Elite Loft Conversions
- Synergy SW Ltd
- Zephyr X
- Harewood Dental Surgery
- Redirack
- Check It Scaffolding
Other Business Categories
- Direct Mail Hampshire
- Exhibition Stands Hampshire
- Personal Injury Solicitors Hampshire
- Gyms & Health Clubs Hampshire
- Massage Hampshire
- Childminders & Babysitters Hampshire
- Community Centres Hampshire
- Agricultural Merchants & Supplies Hampshire
- Woodworking Machinery Hampshire
- Garage Doors Hampshire
- Mobility Equipment Hampshire
- Worktops Hampshire
- Kite Shops Hampshire
- Photocopier Suppliers Hampshire
- Painters & Decorators Hampshire
Season Group in Hampshire, England
Season Group with information like telephone number, maps, postcode, address and related useful information.
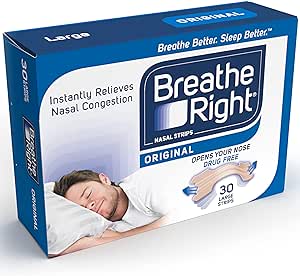
Season Group
Address: 600 Nest Business Park Martin Road Havant Hampshire United Kingdom PO9 5TL
Postcode: PO9 5TL
City/Town: Hampshire, England , UK
Main Phone:023 9248 1923
Website:www.seasongroup.com
Category:General Services
Get simple code & place at your website

Description
Electronic Manufacturing Services
Season Group is a vertically integrated Electronic Manufacturing Services (EMS) provider with manufacturing facilities in USA, Canada, China and Malaysia ? with partner facilities here in UK as well as in Germany.
We have a total of over 600,000ft? of contract electronics manufacturing space and our main capabilities include:
Assembly of complex electromechanical products PCB Assembly (PCBA) Plastic Injection Moulding Plastic Thermoforming (Vacuum Forming) Mould and Tool Making Cable and Harness Assembly After Market Services Design All Season sites are ISO 9001 approved with the following additional certifications being held:
TS 16949 (Automotive) ISO 13485 (Medical) ISO 14001 (Environmental) Facility UL approval for Wire Harness (E95020) and for Cables (E12691)
System Assembly and Test
Our final assembly and test operation makes use of our in-house engineering capability to drive down cost whilst improving quality. For example, as a producer of the plastic parts that are used in complex system assembly solutions, we understand the trade-off between tolerances and product yield. Our design and engineering teams use this type of knowledge to provide detailed Design For Manufacturing (DFM), Design For Test (DFT) and other DFx input during the New Product Introduction (NPI) stage. In addition, our component engineers will utilise their intimate knowledge of our global supply chain in order to identify alternative supply sources ? they will then suggest to our customers in order to drive cost reduction, yield improvement and/or risk reduction benefits.
Our electromechanical assembly capabilities include the following services:
Configure To Order (CTO) Component Traceability Low to Medium Volume batch manufacture Higher Volume flowline and dedicated assembly cell solutions Functional Test ? with the ability to develop and manufacture test jigs in-house HiPot Testing Automated and Semi-Automated Conformal Coating Resin Encapsulation (Potting)
Printed Circuit Board Assembly (PCBA)
Our Printed Circuit Board assembly capabilities are designed to meet all the known requirements of its current and potential customers.
Our PCBA capabilities include :
Dedicated customer cells for higher volume builds Fast changeover Surface Mount (SMT) machines for medium and low volume batch runs with : 0201 placement BGAPlacement to 0.5mm pitch Package-on-Package (POP) placement In-line automated Solder Paste Inspection (SPI) Automatic Optical Inspection (AOI) In-Circuit Test (ICT) X-Ray inspection Automatic Through-Hole Insertion (AI) Manual Through Hole Insertion lines The ability to place components onto a variety of substrates including :- FR4 CEM1 CEM3 Phenolic Polyimide Aluminium
Cable and Harness
The manufacture of products to demanding standards for customers in the automotive, industrial & commercial, security, life safety, clean energy, medical and communications sectors is Season?s strength ? and a key service we offer to these clients is cable and harness manufacture. Therefore, Season has obtained UL site approval for cable production (E12691) and wire harness assembly (E95020). We assemble a full range of cables used including co-axial, shielded, semi-rigid and flat cables.
The products produced require the use of in-house capabilities including:
Double overmoulding Low pressure moulding Insert moulding Waterproof crimping Ultrasonic and resistive welding Large Gauge Crimping up to AWS #1
Plastic Injection Moulding / Thermoforming / Tool and Mould Manufacture
Season has a long history of producing plastics using its in-house capabilities. We see this as a key element in improving quality and reducing Time To Market (TTM) for our customers. Having all the key engineering skills for plastics, cable and harness, PCBA and systems assembly ?under one roof? allows Season to assist customers in all aspects of product commercialisation. In particular, having the ability to design the plastic moulds with the customer, manufacture them in our Tool Room and produce first-off samples in-house really helps us to ensure that final assembly runs smoothly. The added ability to offer both injection moulding and thermoforming (vacuum forming) solutions, also ensures we can give our customers more options to reduce overall lifetime costs and TTM.
Our capabilities include:
Plastic Injection Moulding Class 10k and Class 100k clean room production options Press sizes from 40 tonnes to 1300 tonnes Vertical presses for Insert Moulding Structural Foam moulding Gas Assist moulding In-house secondary processes including Heat Welding, Spraying, Silkscreen, Hot Stamping and Pad Printing Plastic Thermoforming (with Vacuum Forming) Thick Gauge thermoforming Part size up to 1.5m x 2.5m x 0.8m Sheet thickness up to 10mm 6 Axis automated machining Epoxy, wood or aluminium tooling options Thin Gauge thermoforming Sheet thickness from 0.15mm to 2.0mm Tool and Mould Making CNC machine centres Design for manufacturability Mould Flow Analysis CMM Analysis SLA or CNC-machined prototype manufacture CMM machines on-site to ensure accuracy of plastics produced
Global Service Provision
Our customers are looking for the best total cost solution for their products. This may mean using one of our six sites in the Far East, our three sites in North America and/or our two sites in Europe. Customers can ?mix and match? services across sites ? perhaps taking advantage of lower cost manufacture in Malaysia or China for their higher volume products and then using the UK site to provide local assembly services for lower volume, physically large products and/or for Warehousing, After Market or Logistics services.
Our global footprint is:
Havant, UK (with our partner Outsource Electronics) Final Assembly and Test, PCBA, After Market Services, Logistics, Warehousing Dongguan, China Electromechanical Assembly, PCBA, Cable & Harness, Plastic Injection Moulding, Tool and Mould design and manufacture, NPI, Component Engineering and Test Development Penang, Johor Bahru and Kuala Lumpur in Malaysia Electromechanical Assembly, PCBA, Cable & Harness, Plastic Thermoforming and Thermoforming Mould Design Tsuen Wan, Hong Kong Logistics, Warehousing, Final Assembly, Testing and Configuration Shenzhen, China Design Centre San Antonio, Texas, USA Electromechanical Assembly, Prototype PCBA, NPI, After Market Services, Warehousing Toronto, Canada (2 sites) Plastic Injection Moulding, Tool and Mould manufacture, Final Assembly and Test K?lleda, Germany (with our partner Logatec) Final Assembly and Test, After Market Services, Logistics, Warehousing
Find us on Google
Find us on google.co.uk